Hand spun yarns are an absolute joy to work with in so many ways.
I end up with a unique, never to be repeated yarn, which has been spun to highlight the natural beauty of the stitch textures creating a timeless piece of handmade.
With a little bit of knowledge you too can source some unique, natural, high quality yarns and prepare to create your own piece of luxury.
Unique Qualities:
After years of using hand spun yarns I am continually thrilled by their different qualities.
Each spinner’s yarn is totally unique. They can be smooth, textured, thick and thin, one fibre or a mixture of fibres – this is what makes hand spun so special. Using hand spun yarn enables me to create an item, which demonstrates the particular beauty and individuality of that particular yarn.
This is my handspun yarn – Australian Gotland fleece – natural – carded with local Kin Kin alpaca, which I then knitted into an Estonian Lace scarf
I spin a lot of my own yarns, but when I do source other hand spun yarns I always buy them from a person who has spun the yarn themselves. Not only can they can give me a detailed description of the yarn and the fibres used but it also allows me to understand the journey the fibres have been on. This is all part of my sustainable and ethical approach to my craft.
Supply Chain:
I meet so many people who enjoy the rich experience of knowing where things come from. When I am considering a yarn I ask myself the following questions:
• Is it kind to nature? Has its journey been sustainable from seed to yarn, or pasture to yarn.
• Is the colour natural? Colour grown or naturally dyed with nature’s inspiration.
• Does is have a low carbon footprint? Is the wool processed and milled in Australia?
• Is it premium quality? from carefully selected and bred Australian coloured sheep.
In summary – buying and using hand spun yarn is certainly a rich and rewarding experience and will result in a unique long lasting item.
My hand spun yarn is available here.
There are other places to purchase; you can search locally. There may be a local spinning group in your area or a local farm who sell yarns on the side. You could ask around at your local fairs and markets, often people such as myself that regularly use hand spun yarns, are very knowledgeable about local places to source.
CHOOSING WHICH YARN TO WORK WITH
Your spun yarn seller should be able to outline in detail what the fibre is. (Some examples of fibre - wool, cotton, alpaca, silk, camel. They can be pure or blended with each other)
If they can’t, then, unless you are very familiar with the fibre, it is best to feel it before you buy. Then ask yourself, what qualities does the yarn have. Is it soft? Would you wear it against your skin or as an outer garment? This can assist in choosing a compatible pattern to use.
Terms when talking about hand spun yarns:
Like any skilled craft there are many terms to understand when talking about fibres and hand spun yarns.
Click this link to the Glossary under FAQ, for definitions of the following terms:
BLOCKING
CABLE
FELTING
FIBRE
NIDDY NODDY
SCOURING
SPINNING: Over and Under Spinning
SPUN IN THE GREASE
SWATCH/TENSION SQUARE
YARN
What exactly is Ply?
Plying is the process whereby two or more single ply of yarn are twisted together using the “s” twist (anti-clockwise spin of the wheel). What this means is if you overlay the letter ‘S’ over the yarn, the middle bar of the letter mimics the direction of the final twist. This is referred to as Conventional plying; there are a number of different ways to ply.
Conventionally a single ply is prepared using a “z” twist (clock-wise spin of the wheel).
As in everything, these rules can be reversed and plying is a topic of its own!!
The term ply can be confusing, especially in Australia, in that as hand spinners we produce a two, three, four or whatever ply yarn, meaning we have twisted a certain number of singles together. In a commercially spun yarn, ply refers to the relative bulk based on the knitted area you can expect to obtain when using a certain ply equivalent of knitting yarn, not the number of singles plied together. Terminology is further confused by referring to yarns, for example, as DK – equivalent to Australian 8ply. Oh for someone to come up with an international terminology!!
The number of plies affects stitch definition in a variety of ways.
• Single and 2ply – great definition for a drapey, flowing lace that holds its shape.
• 3 ply or more gives a rounder yarn – great for cables and stitch definition with texture. Tends to fill in the holes of lace.
Types of yarn:
Understanding the two main types of yarn will help guide you to choosing the right yarn to get the finish you require. I continually experiment with different types of yarns and recently knitted the woollen style hand spun into lace to see how it affects the finish (see image below).
Worsted/Semi-worsted
Gotland Llama hand spun yarn
• gives a smoother more lustrous denser feeling, drapey fibre
• Crisp popping cables
• Clear stitch definition
Woollen/Semi-woollen
Cheeky hand spun yarn; Estonian lace knitted
The lace definition isn’t as clear but after blocking it will open and create a lusciously soft scarf
• fuzzy, matte, lighter almost fluffy
• May obscure some stitch patterns
• May get fuzzier
• Visually softer, softer to the touch
• Relaxed softer looking cables
• Fills in the holes of lace
HOW TO PREPARE A SWATCH
Now that you’ve chosen and purchased you yarn you can now start your project. But wait! Before I start any project I prepare a swatch (or tension square). This is a simple way to ensure that the item you knit or crochet will be the correct sizing to the pattern you are using. The last thing you want is to spend hours on a precious project to find that it doesn’t fit.
1. Wash your yarn
It’s a good idea to ask your supplier whether the yarn has been washed or not. Washing after spinning sets the twist in the yarn and it allows it to bloom if it wants. If it is not washed it will change the gauge affecting the finished garment.
I always wash my yarn if it has been sitting in my stash for some time, the yarn may have flattened. Washing will allow it to bloom again.
The exception to this is if you are purposely working with yarn that has been spun in the grease, which will create an end product that is partially water proof. Aran sweaters were historically left with the grease in the wool to create waterproofing for the fishermen.
Romney Finn Fleece from Cheeky - Spun in the grease - Final yarn washed after plying.
2. Determine the thickness and metreage of your yarn.
Thickness
First gauge, as accurately as possible, the thickness of the yarn in comparison to commercial yarns.
The following chart is one method that I use to help me do this.
Thickness of yarn Organic Cotton approx metres:
Lace weight/2ply 525
DK/8ply 117
Worsted/10ply 81
An alternative, quick method I use, is the ‘quick eye method’. Take a 60cm length of hand spun yarn and compare the width of its thickest part with that of a similar length of a known ply commercial yarn – pull them both tight (compare same fibre).
Prior to stretching:
Top yarn is commercial 8ply.
Bottom 3 yarns are various weights of hand spun.
After stretching:
Commercial 8ply yarn is second from top.
Hand spun yarns - top is now clearly thicker while the bottom two are slightly thinner.
Metres in the skein:
If you have been given these details, the approximate thickness of the yarn can be determined by referring to the chart above. Patterns will give details of the yarn used and its approximate metre/yard per 50gm of weight.
Yarn tag with approximate meterage.
If not, a handy tool is a niddy noddy skein winder.
a. Weigh the skein of yarn.
b. Wind the yarn once around the niddy noddy (one wrap). Take if off and measure its length. Keep this figure safe as it will be the basis of your calculations whenever you are determining the length of a skein of yarn.
c. Wrap the yarn you wish to determine the metres of around the niddy noddy.
d. Count the number of times that the yarn has completed a full wrap around the niddy noddy.
e. Multiply the number of wraps x length of one wrap (the result of point 1 x result of point 3).
f. This gives you the total length of the yarn wrapped around the niddy noddy in centimetres. Divide this result by 100 to convert the measurement to metres.
g. What to do if your skein weighs more or less than 50gm.
- Divide the metres by the grams, this equals the metreage per gram.
- Multiply the metreage per gram x 50.
Example - Gotland Llama handspun yarn (photo above):
The weight of the skein of yarn is 81gm
The length of one wrap of my niddy noddy = 157cm
The skein of hand spun yarn I am measuring has wrapped around the niddy noddy 89 times.
To find the total length of the skein I multiply 157cm x 89 wraps = 13,973cm.
To convert to metres divide 13,973 by 100 = 139.73 metres say 140 metres.
Determine the length per 50gm:
140 metres divided by 81gm = 1.728 (metreage per gram)
Multiply 1.728 metres x 50gm = 86 metres per 50gm of yarn.
In this example the yarn is roughly worsted/10ply referring to the chart above.
3. Winding yarn from a hank or skein
A tightly wound ball will stretch the yarn but when knitted up and washed the yarn will spring back into shape producing a garment which appears to have shrunk.
Be extra careful not to tension the yarn when winding into a ball, wind it into a soft ball. I use a ball winder to do this, which has been a great investment!
4. Prepare your Swatch
Gotland Opal hand spun
Your tension square should permit for a measurement over a minimum of 5cm (2”) or with heavier yarns, a minimum of 10cm (4”). Generally, hand spun yarn will require a size larger needle than that recommended for commercial yarn.
Problem solving your tension square:
Too few stitches to meet the required tension, your tension is too loose and you need to work with smaller needles.
Too many stitches to meet the required tension, your tension is too tight and you need to work with larger needles.
Choosing a pattern:
Patterns are written in various languages or terminologies – always ascertain where the pattern was printed, this will alert you to having to translate needles sizes and any pattern terms. Particularly with crochet – stitches are vastly different.
There are various things to consider about your chosen yarn when choosing a pattern:
Smooth, firm spinning gives tougher, longer wear – while uneven and knobby spinning may not wear as well as it is inclined to rub and pill.
Hand spun is usually more hairy and has more spring than manufactured yarn, allowances can be made for this by following directions for a size smaller garment than required. Your swatch will determine if this is necessary or needle size change is sufficient.
Natural yarn – either knit the yarn as it presents itself off the fleece or spread the colour evenly throughout the garment. This, in part, will be determined by the person who has spun the yarn. The scarf I am knitting with Cheeky's fleece (as above) has been knitted as presented from the fleece - no prior sorting done.
TIPS FOR USING YOUR HAND SPUN YARN
Spreading the colour evenly:
• Use 2 balls of yarn working two rows with each ball – often this does little more than produce stripes
• Use 3 balls of yarn working one row with each ball and carrying the yarn up the side of the work – a very simple method to assist in spreading the colour.
• If using circular needles reduce this to 2 balls of yarn.
• This method is also ideal for working with yarns of varying textures and scraps of yarn which are different ply equivalents of fibres.
• Circular needles for body and sleeves will also spread the colour using 2 balls of yarn.
Which yarn do I use:
This is generally determined as follows: Plied yarn for knitting and crochet, Single yarn for weaving. But like most rules, this can be broken!
• it is possible to knit with single yarn provided it has not been spun too tightly.
• Too much twist results in the finished garment “cork-screwing” round the wearer, the stitches will slope diagonally and force the fabric to be not square.
• This can be overcome by reversing the movements of the yarn and needles. Knit stitch – knit into the back loop of the next stitch. Purl stitch – purl into the back loop of the next stitch.
• This method can also be used with any yarn and will produce a smoother piece of stocking stitch, a firmer fabric and also assists in tension problems.
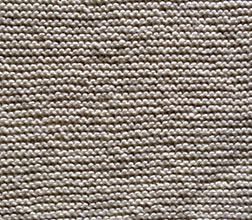
Sample of Andean Mist (thick & thin cotton yarn) knitted into the back loop of the stitch. It has evened out the textured yarn.
Good luck! There is plenty more to learn about using hand spun yarns.
Revisit the tips that my sister-in-law, Kate, gave us in July. The article is under FAQ on my website. Follow this link:
HOW TO SUCCESSFULLY KNIT WITH HAND SPUN YARNS